
Vinyl records have seen a renaissance in the 21st century, and this trend is not slowing down. Demand for this analog medium has climbed over 17 consecutive years, and in 2022, LPs officially eclipsed CDs as the most popular physical recorded music format.
Some speculate that nostalgia has driven the return to the turntable, while others credit Record Store Day for the vinyl revival. Whatever the reason, these five small businesses were inspired by this comeback and are among the few record-pressing outfits in the nation.
Gold Rush Vinyl
In 2017, Caren Kelleher left her role as the Head of Music App Partnerships for Google to pursue band management full time. She found it wasn't for her, but along the way, she noticed the vinyl record resurgence and some accompanying pain points.
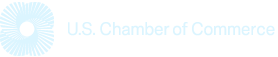
Interested in a small business membership?
Find out how the U.S. Chamber of Commerce can help your company grow and thrive in today's rapidly-evolving business environment. Connect with our team to learn how a small business membership can benefit your bottom line and help you achieve your goals.
Kelleher understood the value of tangible records in a digital world and discovered that the existing technology was in desperate need of improvement. Determined to enhance the quality and efficiency of vinyl pressing, she made her debut in manufacturing as the founder of Gold Rush Vinyl.
Living in San Francisco when she drafted her business plan, Kelleher was energized by the "pioneering spirit of [the] town." In 2018, she opened the pressing plant in Austin, Texas. The small business has gained a reputation for its quick turnaround time — three times faster than the industry standard. It also prides itself on having fewer than 0.05% of records being returned for quality review. To be more sustainable, Gold Rush Vinyl recycles damaged records and scraps by creating vinyl flower bouquets, art installations, and community displays.
Independent Record Pressing
Independent Record Pressing (IRP) of Bordentown, New Jersey, started with six vintage Hamilton Presses made in the late '70s and early '80s. After gaining some momentum, the company upgraded to WarmTone pressing machines that were manufactured between 2017 and 2023. This modernization took them from a manual operation that required timing everything just right to automated production with a smaller margin of error and higher output.
With nine new machines, IRP can make about 2,000 vinyls per device, netting close to 20,000 per day. The facility is climate controlled with new heating and cooling systems tied to around-the-clock monitoring with resource conservation in mind. The small business is putting the wheels in motion for a closed-loop system with a chiller that continually reuses the water that passes through it. The plant also regrinds excess trim cut from pressings to be used for future records.
IRP is Climate Neutral Certified and has invested in hydropower and wind energy, which will offset an estimated 3,308 tons of carbon dioxide equivalents. Artists that have utilized IRP include Radiohead, Iron Maiden, and Tom Waits.
Of all of the things I've done in my life, pressing a record has definitely been the hardest.
Dan Lauricella, New Orleans Record Press
Tangible Formats
Independent recording artist Wesley Wolfe started his business after hitting a dead end in pursuit of a company that would make him just one vinyl record. In 2009, he purchased lathe-cutting equipment from Souri's Automaten so he could do it himself, and it snowballed into Tangible Formats. With no minimum orders and a competitive turnaround time, Wolfe's enterprise appeals to local bands, independent artists and labels, and vinyl DJs.
Tangible Formats stands apart from the crowd because it bypasses the plating and pressing process, cutting directly into blank vinyl. Wolfe has a small workspace and uses a limited selection of gear to transfer digital files to tangible wax. He monitors the quality of the grooves through a scope attached to the lathe and sources discs from Souri's as well.
Wolfe says that frequency limitations contribute to the medium’s signature sound and its upswing in popularity.
"Vinyl is the only way to make sound solid … to bring it into our dimension," Wolfe said in the documentary "Vinyl Nation." He also argues that "record jackets are better to look at than thumbnail images." So in addition to mastering, double-sided recording, and all the packaging, Tangible Formats has also been known to design cover art.
New Orleans Record Press
In 1999, Dan Lauricella moved from Massachusetts to New Orleans. After creating his own record label, he co-founded the city's first vinyl record pressing facility, New Orleans Record Press. With such a rich music culture, Lauricella couldn't believe his business was the only one of its kind in the area.
Before starting New Orleans Record Press, Lauricella renovated homes. In 2016 that's exactly what he was doing with Remi Foulon when they discussed the prospect of building a record press. Lauricella sold a house and pooled the money with Foulon's savings. They found a machine in Canada, fixed it up, and were open for business a year later.
"We have no debt. We have no investors. We built it all ourselves," Lauricella said. He also admits, "Of all of the things I've done in my life, pressing a record has definitely been the hardest. It's so much easier to build a house."
The New Orleans Record Press team is determined to press vinyl for all of New Orleans. They make it a point to host events and give tours of their facility so people can see the process.
Smashed Plastic
Split four ways and aptly situated in the old Hammond organ factory, Smashed Plastic is Chicago's first vinyl-pressing plant in decades. Nestled among coffee roasters, candlemakers, and printing presses in Workshop 4200, its 3,500-square-foot space has been described as having "Willy Wonka factory wonderment." A portion is furnished with a bar, retro arcade games, a vintage jukebox, a brown leather couch, and, of course, albums are spinning all the time.
Getting there took a great deal of research and planning on Andy Weber's part, but he was eager to help smaller bands and labels that may not be prioritized by major presses. So he embarked on this journey, collecting Steve Polutnik and John Lombardo along the way. Astonished by the price of a pressing machine, the fourth co-owner, Matt Bradford, provided critical capital. The group started with one machine, but as demand has grown, so has the production fleet. With the help of Wilco's Jeff Tweedy, Smashed Plastic now has three WarmTone presses.
Through the developments and milestones, this small business remains true to its core. Creating relationships with clients and catering to lesser-known artists are pillars of Smashed Plastic's mission.
CO— aims to bring you inspiration from leading respected experts. However, before making any business decision, you should consult a professional who can advise you based on your individual situation.
CO—is committed to helping you start, run and grow your small business. Learn more about the benefits of small business membership in the U.S. Chamber of Commerce, here.