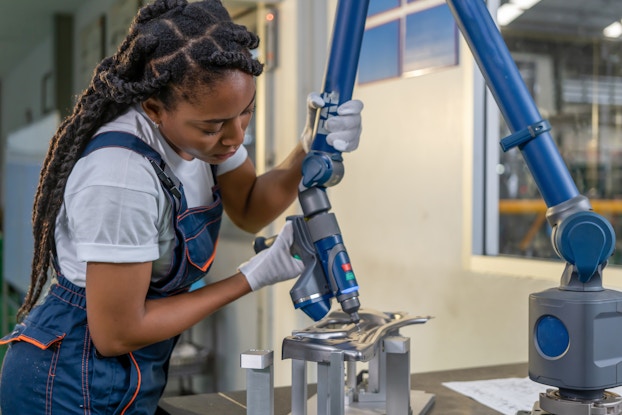
Total manufacturing cost is the metric used to describe the amount your business will spend to manufacture its products. Knowing your total manufacturing cost will help you make better budgeting decisions, find a manufacturing partner, and price your final product for customers.
This guide will help you calculate the costs of manufacturing your product, including what elements to consider and some cost tracking tools that make life easier.
What are manufacturing costs?
Manufacturing costs are defined by Investopedia as “all of the direct and indirect costs businesses face from manufacturing a product or providing a service.”

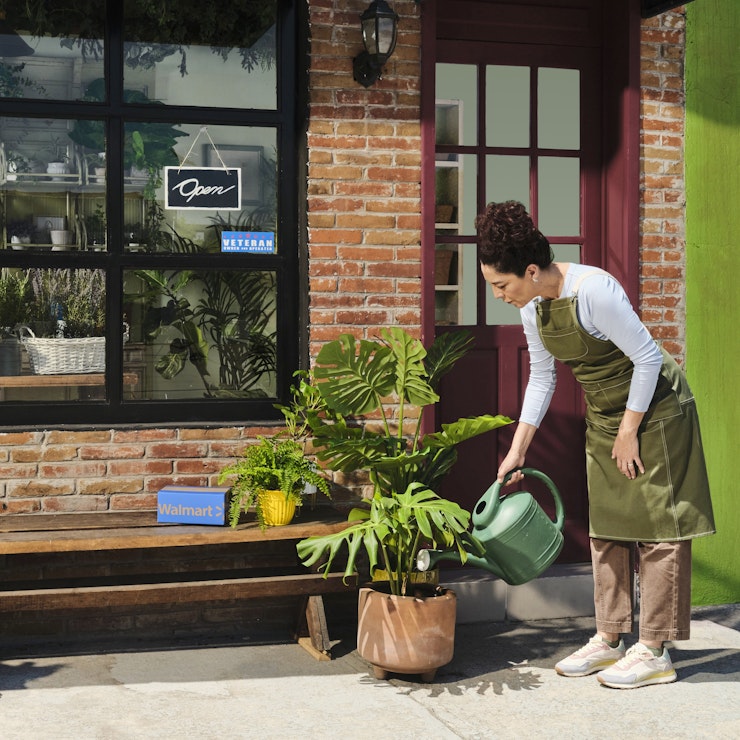
Confusingly, the “cost of goods manufactured” and the “cost of goods sold” are two other metrics that sound similar but refer to different cost categories on an income statement.
Your total manufacturing cost is the total amount of direct material costs, direct labor, and manufacturing overhead spent in a time period.
Cost of goods manufactured only counts products finished during the time period. When the period ends, any unfinished products — those still in production — are considered works in progress. For accounting purposes, these costs are categorized separately.
Cost of goods sold (COGS) is defined only as the manufacturing costs associated with products sold during the time period. This metric excludes any unsold units while still considering the cost of goods manufactured.
Knowing these separate terms is important for accounting, not for vetting different manufacturing partners or setting up your financial forecasts. Total manufacturing cost is the primary metric you’ll need to know for budgeting and planning resource allocation.
Finally, it’s also worth drawing a line between production costs and manufacturing costs. "Production cost refers to all of the expenses associated with a company conducting its business, while manufacturing cost represents only the expenses necessary to make the product," wrote Investopedia.
[Read more: Looking for a Manufacturing Partner? 7 Key Industry Terms to Know]
Your total manufacturing cost is the total amount of direct material costs, direct labor, and manufacturing overhead spent in a time period.
How to calculate manufacturing costs
There are three components to total manufacturing cost: direct materials, direct labor, and manufacturing overhead. These types of production costs, added together, make up the cost of manufacturing your product. Here’s what these types of production costs mean in practice:
- Direct materials: The raw materials that go into creating the final product.
- Direct labor: Expenses related to the employees that create the final product.
- Manufacturing overhead: Any costs related to the manufacturing process that aren’t direct materials costs or labor costs.
Direct materials costs should be distinguished from indirect ones. “Indirect costs do not feature directly in manufacturing the finished product, such as general factory supplies and indirect labor,” wrote the experts at MasterClass. “Indirect costs might also include materials that are part of the finished product but in insignificant amounts per production unit.”
Direct labor costs aren’t limited to simple salary tallies. Direct labor costs may include holiday pay, worker’s insurance, sick leave, and payroll taxes.
Finally, manufacturing overhead is a little trickier to define. “Unlike the other costs, this is a broad category that includes many different items, such as utilities, equipment, etc.,” wrote ProjectManager. “Therefore, first, one must identify these costs, such as the indirect labor and materials costs, add depreciation costs and all other manufacturing overhead costs to get your figure.”
Use a tool to calculate your manufacturing costs
Fortunately, there are software tools that can help you better understand these types of production costs and calculate your total manufacturing cost. Look for enterprise resource manufacturing resource planning (MRP) tools designed to manage production planning, scheduling, and inventory control.
Some popular MRP tools for small businesses include Fishbowl, MRPEasy, and Odoo. There are also enterprise resource planning tools (ERP) that can integrate business functions, including finance, HR, sales, and manufacturing, to give you an overview of costs across the organization.
[Read more: How to Find a Factory to Manufacture Your Product]
CO— aims to bring you inspiration from leading respected experts. However, before making any business decision, you should consult a professional who can advise you based on your individual situation.
CO—is committed to helping you start, run and grow your small business. Learn more about the benefits of small business membership in the U.S. Chamber of Commerce, here.