Published
March 30, 2020
Life in America and around the world has been upended by the coronavirus pandemic. As terms like “social distancing” and “flatten the curve” become part of our daily lives, researchers race to develop treatments and vaccines to fight the virus.
In the meantime, doctors and nurses are on the front lines treating patients. And while they may not realize it, every single patient they treat will be cared for with an array of life-saving products made possible by America’s energy industry.
How is that possible? Well, you may not know it, but natural gas and petroleum-based products are ubiquitous in hospital settings. Oil and natural gas provides the feedstock for advanced plastics which are used to make countless essential medical supplies. One estimate found that an average hospital emergency room has 90 products that are derived from petroleum and natural gas products.
From respirators, gloves, and personal protective equipment (PPE) to sterilization trays, IV lines and ventilation tubes, the battle we are waging against coronavirus is being fought with natural gas and petroleum- based products. The list goes on and on. Life-saving pharmaceuticals. Sanitary, single use plastic medical supplies, devices and other products that limit the spread of infection by reducing contamination. Personal hygiene products such as soaps, detergents, antiseptics and disinfectants that are vital to keeping homes and health care facilities sanitary and safe all are derived from the oil and natural gas. Without these energy-derived products, it is not hyperbole to say that it would be impossible—not just difficult, but impossible—to maintain the modern health care standards we too often take for granted.
How exactly does it work? For many plastics, it begins at what is known as a cracker plant. The rise in domestic energy production has spurred the construction of more than a dozen such new plants, mostly in the Gulf Coast and Mid-Atlantic. These plants convert oil and natural gas into the building blocks for chemicals that become plastics, pharmaceuticals, and advanced materials for use in medical devices, disinfectants, and so much more.
For example, one of the most common types of feedstock is ethane, a liquid found in natural gas. At a cracker plant, ethane is heated to 1500 degrees, which “cracks” it into new molecules that create a substance called ethylene. This ethylene is then transported—usually by pipeline—to a different facility for a process called polymerization. In this process, the ethylene gets converted from a gas to a resin, which can then be engineered and molded into many other plastic products, including all those medical products.
Thanks to our newfound energy abundance, in the last decade alone, more than 300 new chemical and plastics manufacturing facilities have been announced in the United States. Given the sudden uncertain supply chain from overseas, the timing of the energy revolution which fueled this manufacturing boon may prove to be particularly fortuitous to our ability to ease potential disruptions.
Combating the coronavirus will require the U.S. to marshal all of its will and resources. America’s energy industry is doing its part not only by fueling the transport of food, supplies and essential workers, but also by helping to produce the life-saving materials and equipment our healthcare system relies on.
About the authors
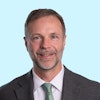
Dan Byers
Dan Byers is vice president for policy at the U.S. Chamber of Commerce’s Global Energy Institute with a focus on environmental and regulatory issues, Byers develops and implements strategies in support of the Institutes broader education and advocacy efforts.